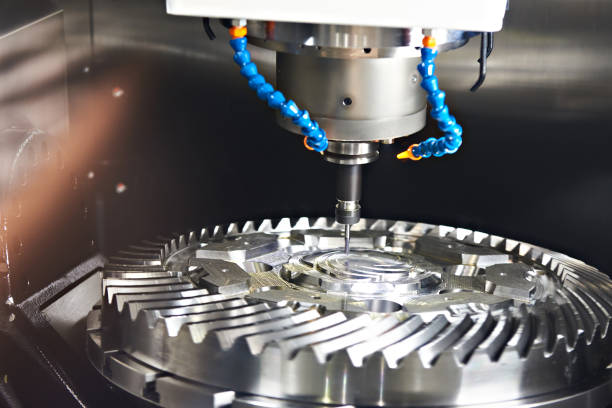
The oil and gas industry relies on high-precision machining to manufacture durable and efficient components that withstand extreme operating conditions. From offshore drilling rigs to refining plants, machining ensures that critical parts function flawlessly under intense pressure, high temperatures, and corrosive environments. Machining for the oil and gas industry plays a crucial role in enhancing operational efficiency, ensuring safety, and extending the lifespan of essential equipment.
This article explores the significance of machining in the oil and gas industry, key machining processes, essential components produced, common challenges, and emerging trends shaping the future of oil and gas manufacturing.
Importance of Machining in the Oil and Gas Sector
The oil and gas sector operates in some of the harshest conditions, where even the slightest component failure can lead to catastrophic consequences. Precision machining is necessary to produce customized, high-performance parts that meet stringent industry standards.
1. Enhancing Equipment Reliability
Oil and gas equipment must endure high stress, extreme temperatures, and exposure to corrosive substances. Machining ensures that critical components meet precise specifications to enhance durability and performance.
2. Customization for Industry-Specific Needs
Unlike mass-produced parts, the oil and gas industry often machining for oil and gas industry requires tailor-made components to fit unique operational requirements. Machining enables the production of specialized parts designed for drilling rigs, pipelines, and processing plants.
3. Reducing Downtime and Maintenance Costs
Unexpected breakdowns in oil and gas operations can be costly. Machined components offer superior wear resistance and longevity, reducing the frequency of repairs and maintenance.
4. Ensuring Compliance with Industry Standards
The industry follows strict guidelines such as API (American Petroleum Institute) and ISO (International Organization for Standardization) standards. Machined parts must comply with these regulations to ensure safety, quality, and efficiency.
Key Machining Processes Used in the Oil and Gas Industry
Various machining processes are employed to manufacture components with high precision, durability, and reliability. These methods help create complex geometries, tight tolerances, and high-strength parts essential for oil and gas applications.
1. CNC Machining
Computer Numerical Control (CNC) machining is one of the most commonly used techniques in the oil and gas industry. CNC machines provide high accuracy, repeatability, and efficiency in manufacturing complex components.
- CNC Turning: Used for cylindrical parts like shafts, couplings, and flanges.
- CNC Milling: Ideal for producing flat surfaces, slots, and intricate geometries.
2. Drilling and Boring
Drilling and boring processes create precise holes in pipeline components, valves, and drilling equipment.
- Deep-hole drilling is used for drill bits, tubing, and structural components.
- Boring operations refine hole diameters to ensure perfect alignment and fit.
3. Grinding and Honing
These processes provide smooth surfaces, enhanced tolerances, and improved resistance to wear. They are commonly used in seals, gaskets, and rotating machinery.
4. Electrical Discharge Machining (EDM)
EDM is useful for machining hardened materials and intricate designs, such as turbine blades and specialized drilling tools.
5. Welding and Fabrication
Many oil and gas components require custom fabrication and welding to achieve strong, durable assemblies for pipelines, offshore structures, and pressure vessels.
Essential Components Manufactured for the Oil and Gas Industry
Precision machining plays a key role in manufacturing a wide range of components used in oil and gas exploration, drilling, refining, and distribution.
1. Drilling Equipment
- Drill bits for penetrating rock formations
- Drill collars to add weight and stability to the drilling process
- Mud pumps for circulating drilling fluids
2. Pipeline and Flow Control Components
- Flanges, couplings, and connectors for leak-proof pipeline assembly
- Valves and seals to regulate oil and gas flow
- Manifolds for fluid distribution
3. Pumps and Compressors
- Centrifugal and reciprocating pump parts
- Impellers and casings to facilitate fluid movement
- Compressor blades for gas processing
4. Pressure Control Systems
- Blowout preventers (BOPs) to prevent well blowouts
- Wellhead components for pressure regulation
- Tubing hangers and casing heads for oil and gas wellheads
5. Structural and Support Components
- Offshore platform parts
- Subsea riser systems
- High-strength bolts and fasteners
Challenges in Oil and Gas Machining
Despite its importance, machining in the oil and gas industry presents several challenges that require continuous innovation and improvement.
1. Machining High-Strength Materials
Oil and gas components require materials like Inconel, titanium, and hardened alloys, which are difficult to machine and cause rapid tool wear.
2. Maintaining Tight Tolerances
Extreme pressure and temperature conditions demand parts with high accuracy and precision, making quality control a challenge.
3. Cost of Production
The rising cost of raw materials, energy, and labor increases the expense of machining high-precision components.
4. Compliance with Strict Industry Standards
Machined parts must meet API, ISO, and ASME regulations, requiring extensive inspection, testing, and certification.
5. Supply Chain Disruptions
Material shortages, global logistics challenges, and fluctuations in demand can affect the availability and cost of essential machining materials.
Emerging Trends in Oil and Gas Machining
With advancements in technology, the oil and gas machining industry is evolving to improve efficiency, precision, and sustainability.
1. Automation and Robotics
Automated machining and robotic systems enhance production speed, consistency, and worker safety in machining operations.
2. 3D Printing for Rapid Prototyping
Additive manufacturing (3D printing) is being used to produce custom components quickly, reducing material waste and production time.
3. Advanced Coatings and Surface Treatments
Innovative coatings improve corrosion resistance, wear protection, and heat tolerance, extending the lifespan of machined parts.
4. IoT and Predictive Maintenance
Smart sensors and IoT-enabled machining equipment monitor real-time performance, predicting maintenance needs before failures occur.
5. Sustainable Machining Practices
Eco-friendly machining focuses on energy efficiency, waste reduction, and the use of recyclable materials to support sustainability efforts.
Conclusion
Machining for the oil and gas industry is essential for producing high-precision, durable components that support drilling, refining, and transportation processes. With advanced CNC machining, drilling, grinding, and fabrication techniques, machining ensures that oil and gas equipment remains efficient and reliable.
Despite challenges such as high material costs, stringent regulations, and machining complexities, continuous innovation in automation, additive manufacturing, and predictive maintenance is transforming the industry. These advancements are shaping the future of oil and gas machining, improving efficiency, safety, and sustainability in energy production.