In today’s fast-paced industrial world, ensuring safety in manufacturing processes is of utmost importance. Custom CNC (Computer Numerical Control) machining has emerged as a vital technology in parts manufacturing, offering unparalleled precision, efficiency, and safety. This article delves into how custom CNC machining enhances safety in manufacturing processes, focusing on key aspects that make it indispensable for modern industries.
The Role Of Custom CNC Machining In Manufacturing
Custom CNC machining parts manufacturing involves using computer-controlled machines to fabricate components with high precision. Unlike traditional manufacturing methods, CNC machining minimizes human intervention by automating complex tasks. This technological leap has not only increased productivity but has also transformed safety standards in the manufacturing sector.
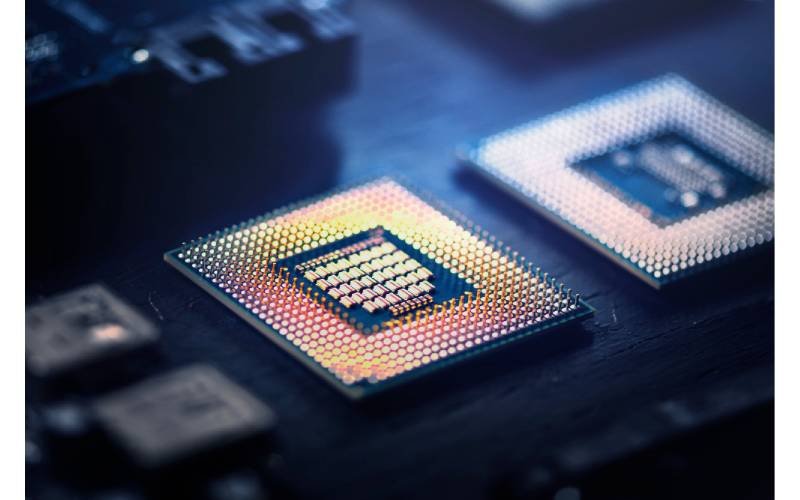
Key Safety Challenges In Traditional Manufacturing
Before exploring the safety benefits of custom CNC machining, it is essential to understand the risks inherent in traditional manufacturing processes:
- Manual Handling Risks: Traditional methods require extensive manual operation, increasing the likelihood of injuries from repetitive strain or mishandling of tools and materials.
- Precision Errors: Human errors in manual machining can lead to defective parts, which may compromise product safety and lead to accidents.
- Exposure to Hazards: Workers are often exposed to sharp tools, moving parts, and hazardous materials, heightening the risk of accidents.
- Inefficient Workflows: Poorly designed workflows can lead to fatigue, stress, and mistakes, further endangering worker safety.
Custom CNC machining addresses these challenges by integrating advanced automation and precision technologies into manufacturing processes.
How Custom CNC Machining Enhances Safety?
1. Minimized Human Interaction
Custom CNC machining parts manufacturing significantly reduces the need for manual intervention. Operators program the machines to perform tasks, which are then executed with minimal human involvement. This reduces the risk of:
- Accidental injuries caused by manual tool handling.
- Fatigue-related errors.
- Exposure to hazardous materials and equipment.
2. Precision and Consistency
CNC machines are designed to deliver high levels of accuracy and repeatability. This precision ensures that components are manufactured to exact specifications, minimizing the likelihood of defective parts. Accurate parts reduce safety risks in end-use applications, such as:
- Aerospace components where precision is critical to prevent catastrophic failures.
- Automotive parts that must meet stringent safety standards.
3. Enhanced Machine Safety Features
Modern CNC machines come equipped with advanced safety features, including:
- Enclosed Workspaces: Machines often feature protective enclosures that shield operators from moving parts and debris.
- Emergency Stop Systems: These systems allow for immediate shutdown in case of anomalies, preventing accidents.
- Sensors and Monitors: Real-time monitoring systems detect issues like overheating, tool wear, or material anomalies, ensuring safe operation.
4. Reduced Material Waste and Hazard Exposure
Custom CNC machining optimizes material usage by reducing waste, which lowers the chances of accidents caused by handling excess scrap. Additionally, it minimizes the need to work with hazardous materials directly, as machines can handle these processes autonomously.
5. Streamlined Workflow and Automation
Automation provided by custom CNC machining eliminates inefficiencies in workflows, allowing for:
- Faster production cycles with reduced worker fatigue.
- Simplified task management, ensuring workers focus on overseeing operations rather than performing physically demanding tasks.
- Improved workplace organization, reducing trip hazards and clutter.
6. Error Reduction Through Simulation
Before the actual machining begins, CNC software allows manufacturers to simulate the entire process. This simulation:
- Identifies potential errors or collisions in the machining process.
- Enables adjustments to be made before production begins, ensuring smoother operations.
- Prevents costly and dangerous mistakes that might arise from trial-and-error methods.
7. Improved Training and Skill Development
Custom CNC machining reduces the complexity of operations, making it easier for workers to learn and adhere to safety protocols. Training operators on CNC systems focuses more on programming and supervision rather than physical handling of tools, fostering a safer work environment.
Applications Of Custom CNC Machining In High-Safety Industries
Industries with stringent safety requirements benefit greatly from custom CNC machining parts manufacturing:
- Aerospace: Ensures the production of precise components to meet rigorous safety and performance standards.
- Medical Devices: Facilitates the creation of intricate and reliable parts for surgical instruments and implants.
- Automotive: Enhances the safety of vehicles by manufacturing critical components with exact specifications.
- Defense: Produces durable and precise parts for military equipment, ensuring operational reliability and safety.
The Economic Benefits Of Enhanced Safety
Improving safety in manufacturing processes through custom CNC machining also offers significant economic advantages:
- Reduced Downtime: Fewer accidents mean less downtime for investigations and repairs.
- Lower Compensation Costs: Enhanced safety reduces the likelihood of worker injury claims.
- Improved Reputation: Companies that prioritize safety attract more business and retain skilled employees.
Future Innovations In Custom CNC Machining
As technology advances, custom CNC machining will continue to enhance safety through:
- AI Integration: Machine learning algorithms will predict and prevent errors, ensuring even safer operations.
- Collaborative Robots: CNC systems will work alongside human operators more seamlessly, enhancing productivity and safety.
- Remote Monitoring: Operators will oversee machining processes from a safe distance, further reducing risk.
Conclusion
Custom CNC machining has revolutionized parts manufacturing by elevating safety standards across industries. By minimizing human interaction, ensuring precision, integrating advanced safety features, and streamlining workflows, this technology has become a cornerstone of safe manufacturing practices. As industries continue to adopt and innovate upon CNC technology, the future promises even safer, more efficient manufacturing processes. Investing in custom CNC machining is not only a step towards improved productivity but also a commitment to creating a safer work environment for all.